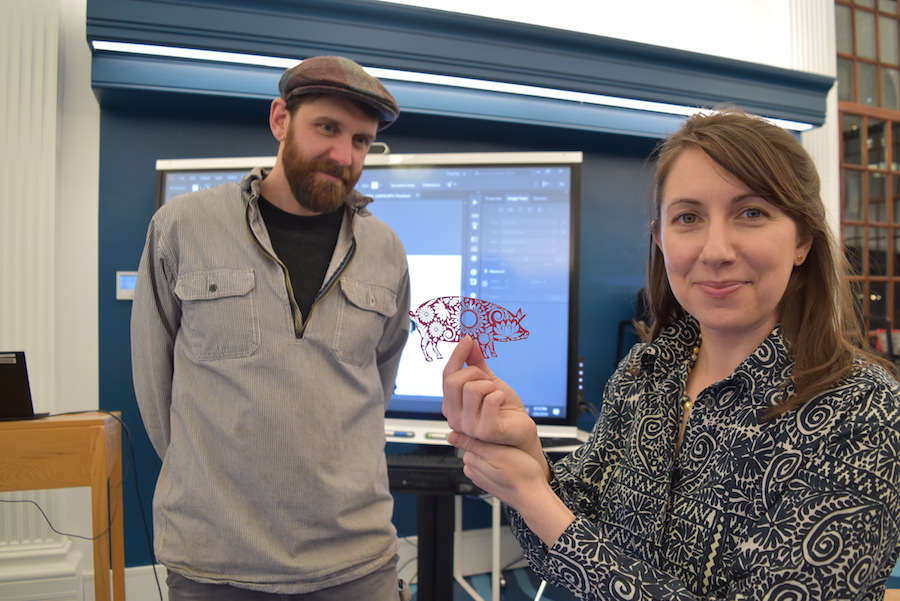
Downtown | MakeHaven | New Haven Free Public Library | Arts, Culture & Community
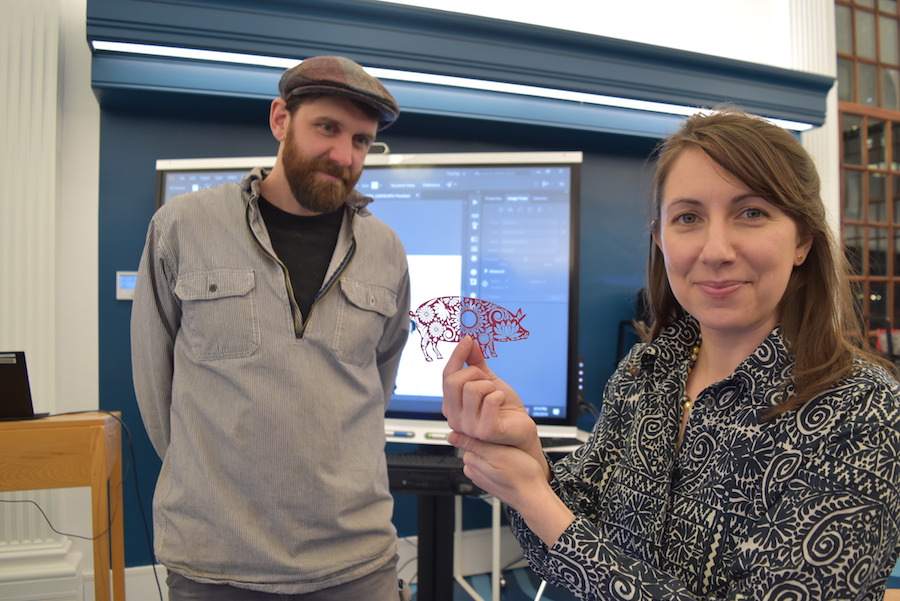
Creatives In Residence Ryan Paxton and Jacquelyn Gleisner. Leah Andelsmith Photos. |
Jacquelyn Gleisner peered into a 3D printer, watching bright purple strands of plastic build up layer by layer. In another corner of the room, several library patrons huddled around a big, grey machine, watching as a laser carved intricate designs into a sheet of red card stock.
Nearby, Ryan Paxton pulled a fresh sheet of slick, black stickers from the vinyl cutter and laid them next to a stack of engraved, wooden keychains.
Gleisner and Paxton are the new Creatives in Residence in the Tinker Lab, a brand new makerspace at the New Haven Free Public Library’s recently completed innovation project, Ives Squared. The Tinker Lab joins Make Haven—an established makerspace that recently moved into new digs at 770 Chapel St.—as the downtown anchors in New Haven’s budding makerspace eco-system.
While other spaces exist—there's the decades-old Eli Whitney Museum & Workshop just over the Hamden town line, and a smaller makerspace in the Jewish Community Center in nearby Woodbridge—these are both central, located less than half a mile away from each other.
A makerspace—sometimes called a hackerspace—is a creative space with the supplies and equipment needed to make any number of crafts or projects. The definition is broad, and equipment can range from Legos and cardboard to top-of-the-line printers, while locations include garages and schools. The space is usually shared, and many believe the most important components of a makerspace are the people who come together inside it and the skills and creativity they bring to the table.
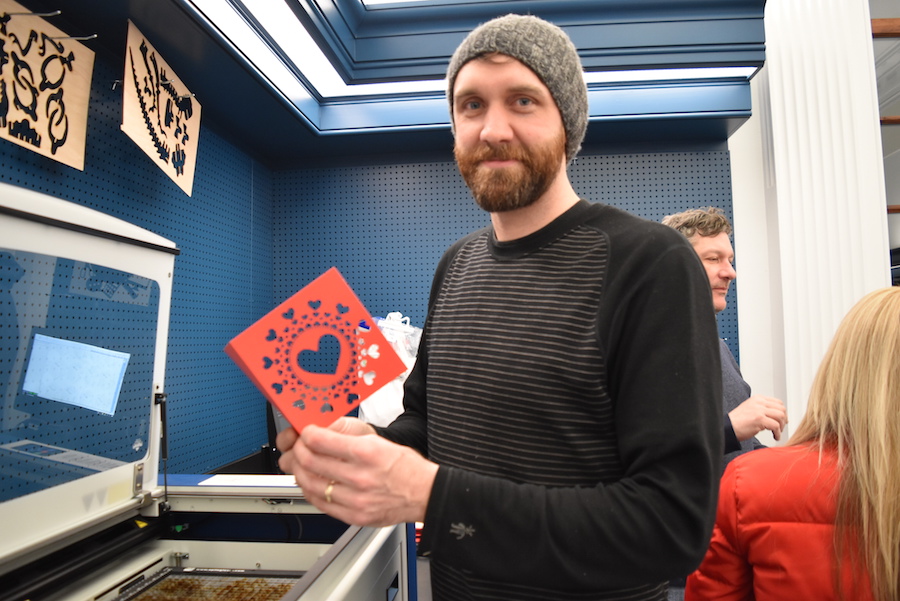
Ryan Paxton with a laser-cut valentine. Paxton works at the Eli Whitney Museum and Workshop as the Senior Shop Manager and Digital Fabrication Supervisor. |
“We’re the front door for people,” said Gina Bingham, NHFPL business outreach librarian, during a recent open house at Ives Squared. “Our machines are meant to be comfortable for beginners.”
As Creatives in Residence (CIRs), newlyweds Paxton and Gleisner—who make art together using some of the same technologies found in the Tinker Lab—will be offering weekly classes in the Tinker Lab through June. They’re taking inspiration from the resources in the Tinker Lab. At one February workshop, for example, participants have an opportunity to make delicate valentines using the precision of the laser-cutter.
Other available equipment includes crafting supplies like sewing machines, button makers and jewelry-making tools; electronics and programming kits like Arduino and Raspberry Pi; and maker toys like Keva blocks and a Meccano erector set. Classes are free to participants, as are the materials used during instruction.
“It can be intimidating sometimes, especially if you don’t have a background” in this type of work, Gleisner said. “I think a lot of people think they could never do it, but it’s accessible to a broader swath of the population than people think.”
Touring the space, Paxton emphasized that patrons can walk away from the Tinker Lab with real, transferrable skills that they can use in shops with similar but more advanced machines, or even in the workplace.
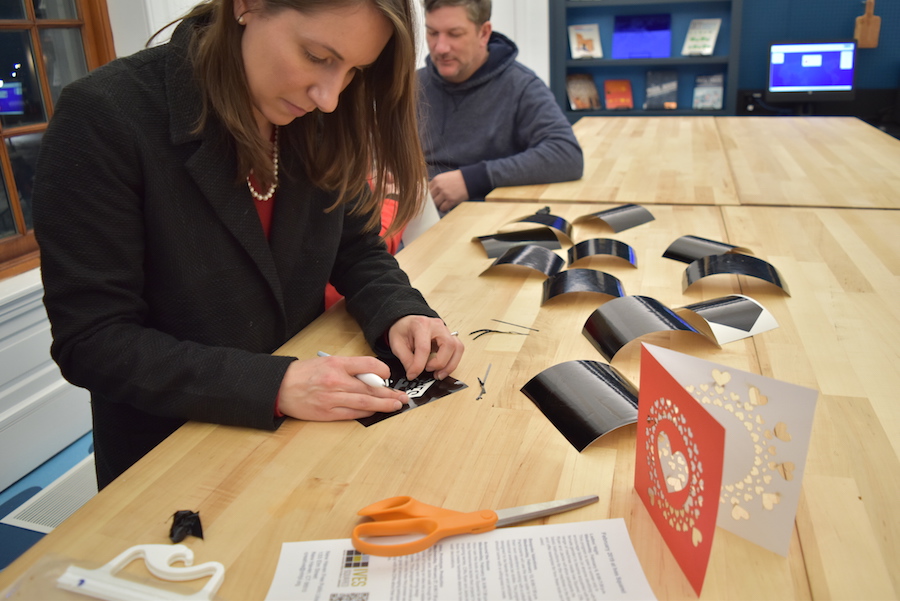
3D printers and Computer Numerical Control (CNC) machines—like the Tinker Lab’s Carvey, which carves and engraves wood, plastic, and other materials—can be used in manufacturing. Laser and vinyl cutters can be used in digital fabrication. And the software that powers these computer-controlled machines is also used in graphic design and architecture.
“You could go into a shop and say, ‘I do know how to use this machine,’” Paxton said. “All the machines could be related to jobs. If you get good at it, these are skills you could take with you.”
The Tinker Lab community has grown steadily over the last six months—Bingham said that busy days see between 70 and 100 people using both sides of Ives Squared, and over 200 people are certified to use the machines solo. As tinkerers become more advanced, the library refers them to other spaces in the maker eco-system, primarily Make Haven.
In the early 2000s, Make Haven started as a simple meetup group of makers and hobbyists. Once the group decided they wanted to get serious about creating a collaborative space, members who could donated $50 a month until there was enough to purchase a brick-and-mortar space at 266 State Street in 2012. When the group outgrew that space, they raised the money needed to expand and move into their current 4,100 square-foot shop at 770 Chapel last August. Now there are 260 members and a new co-working space for start-ups who also need a makerspace.
“Now we’re working on sustainability at our new, larger size,” Chief Maker J.R. Logan said during a recent tour and interview.
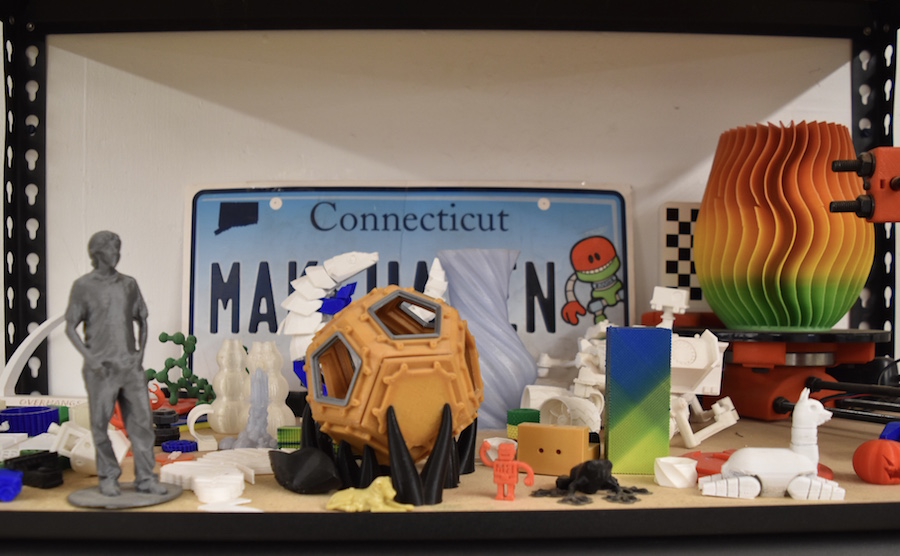
Walking through Make Haven’s new workshop, both the variety and the depth of Make Haven’s offerings are on display. There’s HAM radio equipment, an embroidery machine, a bike repair station, and even an antique proofing letter press, rescued from a rusty demise in a Hamden backyard.
There’s a vacuum former for making masks and molds, an electronics work bench where members can solder their own circuit boards, and a set of computers with a suite of professional design software like Inkscape and Meshlab.
There’s a large wood shop with heavy-duty equipment like a lathe, band saws, and a planer, as well as two CNC machines that dwarf the library’s Carvey. Badges are required to operate much of the equipment and are earned by learning how to use the tool safely and care for it properly. Members bring their own materials to work with, and volunteers are on hand six nights a week to assist or instruct.
“For the most part it’s clean up after yourself and help it be sustainable,” Logan said, showing off a cupboard full of well-kept, wood working hand tools. “We try to balance the freedom to make things with structure for safety and coordination.”
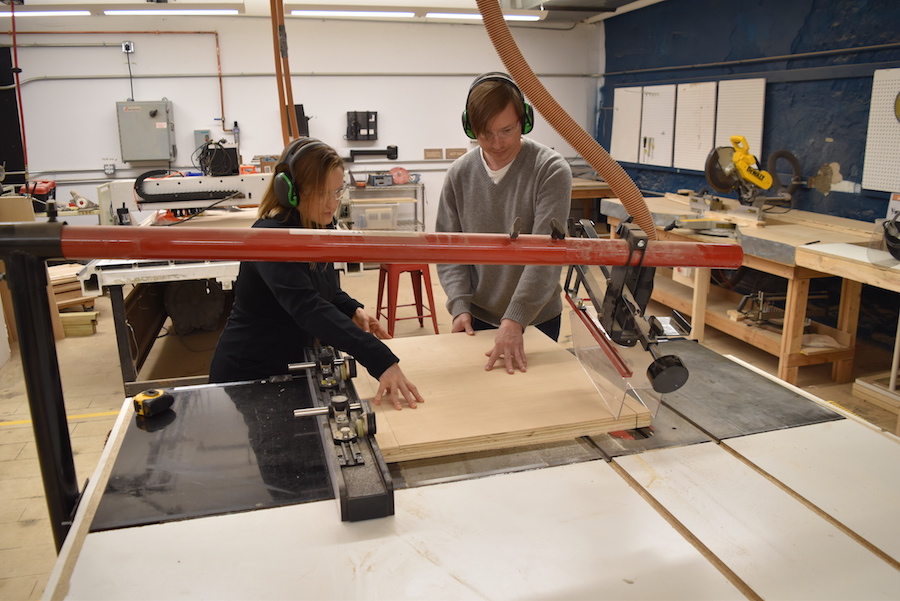
Valery and Rick Lawson. |
On a recent Friday, New Haveners Valery and Rick Lawson were using the table saw in the wood shop, making a combination cabinet-dining table to furnish their tiny apartment. Rick, who’s been a member for three years, used his wood shop badge to unlock the machine while Valery assisted as his guest. The pair guided a large sheet of plywood through the blade, watching carefully through safety glasses. Sawdust clouded the air as their protective ear muffs blocked the loud droning of the machine.
Living in a small space at home, they said they find it difficult to store their own tools—“even little things add up, even a hot glue gun”—or find wide, open table space to work on. Membership is $50 a month (there are fellowship and scholarship opportunities available, as well as student discounts) and Lawson said the price is worth it for him.
“I couldn’t afford to buy the tools on my own,” he said.“It’s fun for us to have access to these tools as part of what we do” as artists.
Also using the space was New Haven resident Nick McGhee, who recently competed in NASA’s 3D-printed Habitat Challenge and placed among the top ten teams. He said Make Haven was “indispensable” in the process, from using the 3D printer to create the model, to having 24/7 access to the space, to working with fellow members willing to weigh in and contribute to the project.
Sidling up to Make Haven’s brand new quilting frame and accompanying CNC quilter, Logan explained that the organization is “very much like a co-op” in that development of the space is driven by member interest. If the 3D printer is broken or folks are confused about how to use the laser cutting software, Logan learns what he needs to do in order to help.
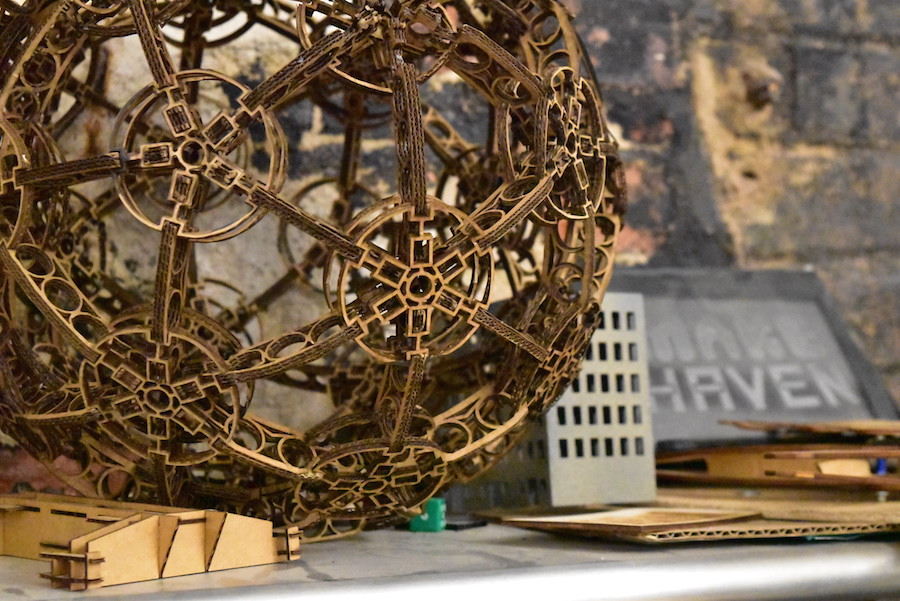
“I get excited about adding new capabilities to the space. I find myself experimenting and learning to use equipment as we get it on board,” he said.
On a recent Thursday, a group of eight printmaking students gathered around artist Michael Angelis as he spread deep, red ink on a glass counter top, demonstrating how to roll a brayer into it. He taught the class to recognize the sticky sound a perfectly-coated brayer makes and the peaks and valleys that appear in the swath of color on the glass when the ink is evenly distributed.
A volunteer cranked the printing press, then revealed a wood block print of a cart with spindly wheels. Madison illustrator Bob Shea took note of the settings on the press before running his paper through. He’s been a Make Haven member for 15 months.
“I love it,” he said. “Any stuff you see on YouTube, you can come in and make it.”
Attendees took turns setting the press to get the right amount of pressure, rolling their prints through, and evaluating or admiring the results.
“When I moved to New Haven, it was a perk of the city,” attendee Shannon Burke said as she waited for her turn at the press. After moving to the city four months ago, she enjoys communicating with other members through Make Haven’s set of Slack channels, getting help and advice when she needs it. She wants to learn how to use the resin printer, which makes shapes you can’t create on a 3D printer.
“I knew three people when I moved here. It’s nice to talk to people you don’t work with,” she said. “The more you come, the more of a community it will be.”
Trial And Error
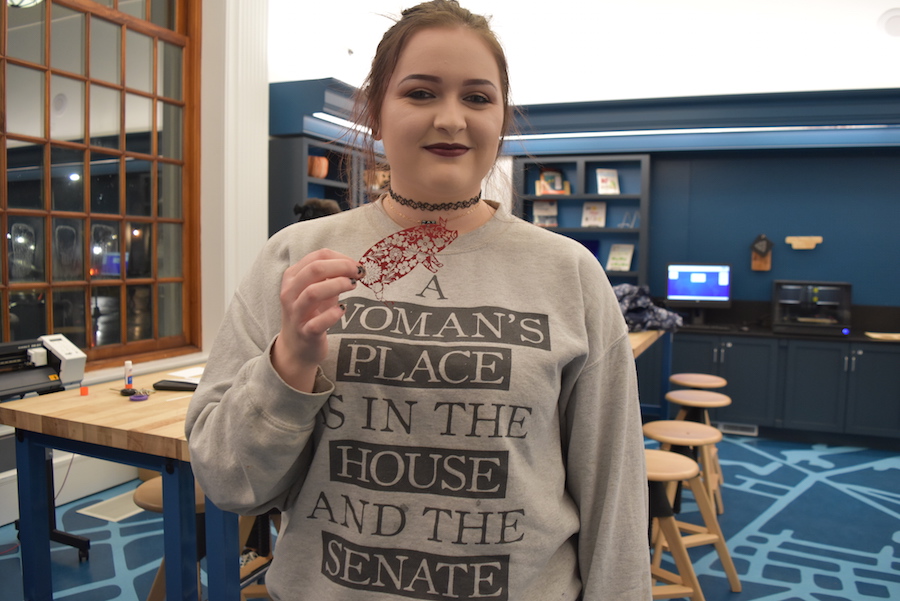
Katie Heinlein with her laser-cut creation. |
Up Chapel Street and across the New Haven Green just a few days later, a half-dozen library patrons gathered at the Tinker Lab computers during Gleisner and Paxton’s recent Ladies’ Night event—a chance for women and non-binary folks to get an introduction to the space. Their inspiration was a paper cut-out Gleisner and Paxton made using the laser cutter: a red boar with a delicate filigree of spirals and flowers carved out from its shape. Attendees opened Adobe Illustrator and got ready to start their designs.
“The idea is to give the cutter a line to follow,” said Paxton, showing everyone how to trace images. Participants needed to think about both the positive and negative space in their designs, and about what which parts of the paper would be left behind each time a cut is made.
“I don’t work digitally,” said Katie Heinlein, one of Gleisner’s students at the University of New Haven. Heinlein has a painting background and likes fiber arts. However, a laser cutter assignment in her digital fabrication class meant she had started learning Adobe Illustrator just a few days prior. Ladies’ Night offered another chance to practice.
Heinlein’s pig was a riff on Gleisner’s, incorporating new images she pulled from Google and modified with Illustrator. She leaned over the laser cutter, looking through the glass cover and capturing the machine’s rapid process with her cell phone camera.
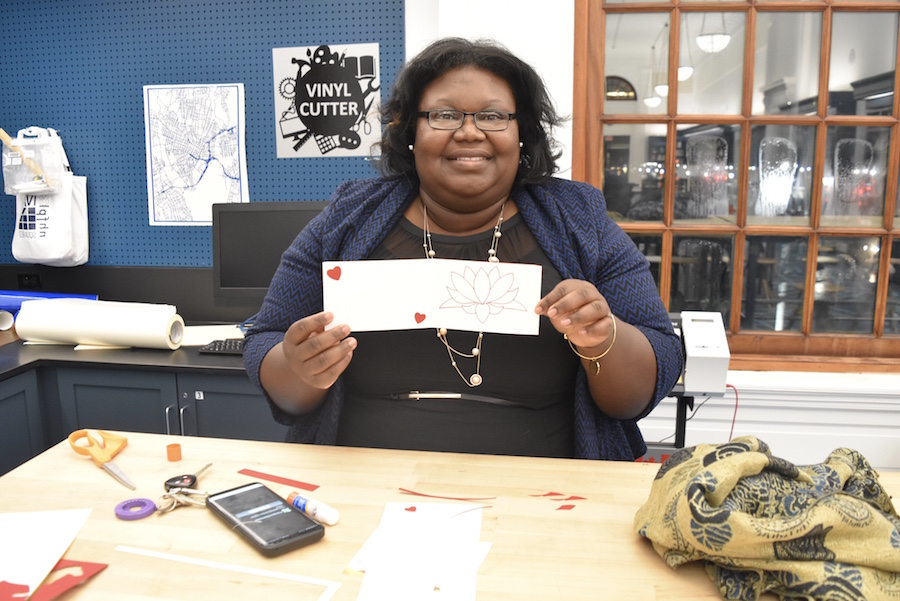
Noreia Savage with her laser-cut creation. |
Heinlein watched as the areas of her design with the tiniest details ended up as empty spaces. Apparently, if there are too many lines too close together, the laser ends up burning a hole in the material. But trial and error is part of the process of learning a new medium and Heinlein shrugged it off.
“I’m just learning this semester, but I definitely want to keep using it,” she said. “The fact that this is here and free is really cool.”
Noreia Savage, who recently moved to New Haven from Hartford, found out about the event on Facebook and brought her mentee Iyonna along. The pair’s creations accidentally came out pencil-line thin and very delicate. Savage glued her lotus flower design onto a card, using the shapes that were removed from the paper to create an abstract composition. Iyonna was pleased with her dainty, laser-cut puppy and said she would definitely be back.
“I don’t usually do stuff like this,” she said. “It’s good to learn something new.”